Tipos de mantenimiento industrial
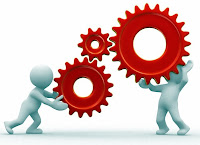
Esto es un post completamente off-topic, pero ya sabéis que de vez en cuando escribo de lo más inesperado. Los blogs personales son así. A lo que iba, que aquí va una reflexión sobre la historia del mantenimiento en la industria, a través de su evolución en diferentes tipos.
MANTENIMIENTO CORRECTIVO
La revolución industrial trajo consigo las primeras fábricas modernas a finales del siglo XVIII, y estas fábricas estaban llenas de máquinas. Las máquinas fallan, se averían y se rompen; es decir, dejan de producir. Antes eso no era un gran problema, porque los procesos eran lentos y manuales, y una interrupción de la producción no ocasionaba grandes pérdidas. Por eso, y por la propia simplicidad de esas máquinas primitivas, estas podían ser reparadas por los propios operadores.
Sin embargo, cuando los procesos de producción se aceleraron y las máquinas se hicieron cada vez más complejas y costosas, empezó a asociarse el tiempo de parada con pérdidas económicas, y se hizo patente la necesidad de acortar esos tiempos de inactividad forzosa. Esto dio origen a los primeros departamentos de mantenimiento, compuestos por mecánicos especializados, con conocimientos y habilidades que los operadores no tenían.
Estos primeros operarios de mantenimiento intervenían solo en caso de fallo, y su intervención se limitaba a volver a poner la máquina en marcha. Esta forma de mantenimiento fue predominante durante muchos años, hasta que más o menos en la década de 1920 la industria empezó a demandar tiempos de parada cada vez menores. La competencia era cada vez mayor, y se hizo evidente que los procesos productivos eran más rentables cuanto más fiables.
MANTENIMIENTO PREVENTIVO
Hay dos formas de acortar los tiempos de parada: acelerar la reparación o disminuir las paradas no programadas. El mantenimiento preventivo busca el segundo punto, y su objetivo último es que una planta nunca tenga que parar de forma no programada. Para conseguir esto, se hace un estudio de la durabilidad de las diferentes partes de una máquina, y se fuerza su reparación o reemplazo antes de que se produzca la avería.
Por ejemplo, si la vida útil de un rodamiento son 5.000 horas, el mantenimiento preventivo aconseja cambiar ese rodamiento antes de llegar al final de su vida útil. Este cambio se hará antes o después dependiendo de varios factores, como la criticidad del equipo y el tiempo y coste de la operación. Es decir, el reemplazo del rodamiento se hará antes si la máquina es importante y puede ocasionar una parada de toda la planta, si es una pieza barata o si su cambio es una operación larga y dificultosa. Por contra, se buscará alargar su vida útil si se trata de una máquina poco importante, una pieza cara o si su intercambio es rápido y sencillo.
En definitiva, se busca que las máquinas estén siempre en buen estado, consiguiendo que la probabilidad de avería se reduzca lo más posible. De esta forma, las máquinas son más fiables y la producción se puede planificar.
MANTENIMIENTO PREDICTIVO
El mantenimiento preventivo no es la panacea, ya que muchas veces se cambian piezas que aún están en buen estado. Cuando los costes de mantenimiento empezaron a ser una parte importante de la economía de las empresas, en un entorno cada vez más competitivo, se vio la necesidad de disminuir estos costes para dar una ventaja competitiva a la empresa. Así, el siguiente paso es cambiar una pieza justo antes de que se produzca el fallo.
Hay varios métodos para monitorizar el estado de una máquina. El análisis de vibraciones permite conocer el estado de rodamientos y otras partes móviles, principalmente partes giratorias. Las termografías permiten apreciar incrementos de temperatura en partes móviles, que suelen indicar un problema a punto de convertirse en avería; y también permiten evaluar el estado de equipos eléctricos. Las lámparas estrobóscopicas permiten observar partes giratorias como si estuviesen paradas, de forma que se pueden apreciar daños físicos como fisuras o roturas.
Conociendo el estado real de las partes críticas de una máquina pueden organizarse paradas programadas en las cuales se ejecutan varias operaciones de mantenimiento de forma simultánea y además de forma optimizada gracias a la preparación previa. También se puede programar mantenimiento de oportunidad, teniendo todo preparado para cambiar la pieza dañada cuando la instalación pare por cualquier otro motivo.
La implantación de este tipo de mantenimiento aumenta los costes fijos, debido a la necesidad de instrumental y personal especializado. Sin embargo, una vez se ponen en marcha las rutas de inspección, los costes variables de mantenimiento caen y la producción aumenta. En ese momento las empresas suelen tener la tentación de reducir el personal especializado que puso en marcha el nuevo sistema, lo cual pone en grave riesgo los avances logrados ya que el mantenimiento predictivo es un proceso continuo que va más allá de la implantación inicial.
MANTENIMIENTO PROACTIVO
En los últimos años está surgiendo un nuevo tipo de mantenimiento que busca reducir las intervenciones del departamento de mantenimiento pasando parte de sus funciones al operador de la máquina. Según esta corriente, el operador debe hacerse responsable de las tareas simples de mantenimiento que no requieren de una gran especialización. Por ejemplo, el operador puede engrasar partes de la maquinaria, ajustar sensores o incluso cambiar partes que se desgastan con frecuencia.
Es una filosofía curiosa, ya que parece un retorno a los orígenes del mantenimiento, cuando este era ejecutado por los propios operadores de la máquina. Sin embargo, esta técnica pueden tener resultados sorprendentes si se organiza adecuadamente, reservando las tareas complejas para el personal de mantenimiento y motivando al operador para que se preocupe por el estado de los equipos bajo su control.
CONSIDERACIONES FINALES
Por cierto, habría que hablar también del engrase, que al principio era ejecutado por el propio operador, pero que pronto pasó a ser realizado por personal especializado. Este personal, en plantas lo suficientemente grandes, podía dedicarse al engrase en exclusiva, realizando rutas de engrase diferentes cada día, y cubriendo puntos de engrase de distinta periodicidad. Con un uso adecuado de herramientas informáticas de organización del mantenimiento, el engrase de una planta puede ser optimizado hasta la garantía total, y con la formación adecuada puede conseguirse incluso que el engrasador ejecute tareas de mantenimiento predictivo al mismo tiempo que completa sus rutas.
No sé si lo he dejado claro en este post, pero la organización del mantenimiento industrial es un campo muy interesante, y que puede tener beneficios que muchas empresas no se atreven ni a soñar: mayor eficiencia de las instalaciones productivas a un menor coste, y aumentando de paso la calidad y la seguridad. Con un poquito de inversión extra, los beneficios con más que evidentes.
Todo esto está basado en mi experiencia en el sector, tras cinco años como ingeniero de mantenimiento de una planta industrial de tamaño medio, ejerciendo distintas funciones como técnico, planificador, coordinador de preventivo y preventivo, y finalmente jefe de mantenimiento. A nivel laboral, fue una época apasionante, pese a que el ritmo de trabajo era muy alto. Los trabajos de oficina, monótonos a más no poder, me aburren rápido. En un fábrica, sin embargo, siempre hay nuevos retos y problemas. Esa exigencia, junto con buenos compañeros y algunas anécdotas, es el clima perfecto para ser feliz en el trabajo.
Creo que algo similar nos enseñaron en la escuela técnica para reparación de PC's.
ResponderEliminarLos métodos, cuando se hacen bien, se pueden aplicar a cualquier campo :)
EliminarA mi me lo enseñaron en la asignatura de calidad, yo creía que esa asignatura sería de como comprobar la calidad de materiales, pero era de como optimizar la empresa y el trabajo. Nos explicaron este tipo de conceptos y normativa ISO entre otras.
ResponderEliminarAprovecha bien esas asignaturas, que aunque ahora te puedan aparecer aburridas en realidad son muy útiles. ¡Cómo me gustaría regresar a la universidad a aprender cosas nuevas!
Eliminar